ATTENTION GROS DOSSIER!!!!!!!!!
Comment faire évoluer sa prusa i2 pour être a la hauteur d’une i3 sans tout racheter ni recommencer!!
Et ce à moindre frais puisqu’il vous faudra seulement de nouvelles pièces imprimées, et un cadre en aluminium de préférence…
Pour commencer je vous Présente la victime:
elle a été montée en bowden pendant un temps,
puis des problèmes soudains de qualité m’ont fait douter et j’ai remis l’extrudeur sur le chariot, d’où le câblage le long du tube teflon. Ces mêmes problèmes m’ont mené a coupler une deuxieme alim et à éclater le faisceau électrique que j’avais fait, tout ça pour finalement se rendre compte que cela venait de la bobine d’abs que j’utilisais qui était de très mauvaise qualité.
Quoi qu’il en soit il y a des modifs qui me démangent depuis un certain temps, il est temps de passer a l’action:
Le but est passer en axe des X vertical et de rigidifier le châssis en Z, le tout sans toucher au plateau (Y) ni a la partie principale du chassis formée par les tiges filetées et les vertex.
J’avais déjà des fichiers CAO d’une prusa sous la main que j’adapte au fur et a mesure de mes modifs, ils ont servi de base à celle la aussi.
J’ai cherché un peu sur le net pour un axe vertical à adapter sur i2 mais je n ai pas trouve mon bonheur, les x-ends de i3 ne sont pas compatibles non plus sans modifier le châssis radicalement, alors je les ai dessinées comme je les voulais!
Ils peuvent paraitre imposants mais n’utilisent pas tant que ça de plastiques et sont plutôt légers compare à leur gabarit. Le cahier des charges ici est durabilité et efficacité, pas l’optimisation du temps d’impression ni l’économie de plastique pour produire facilement en masse. Une fois tout assemblé, l’axe des X est mieux équilibré lorsqu’on le tient par les supports de roulements.
Le chariot également, est fait sur mesure et adapté à ma configuration spécifique, ma courroie de récup exotique (larg. 10mm, pitch 3mm) et son pignon qui ne l’est pas moins s’alignent désormais parfaitement avec des fixations sans vis, et tendeur intégré.
J y ai également ajouté une encoche pour passer la grosse transmission sans ajouter de cale sous l extrudeur.
les supports moteur de Z sont basés sur les modèles d’origine i2, j’y ai simplement ajouté une fixation pour le cadre rigide (4mm tête fraisée)
On voit bien le cadre largement inspiré de la i3 qui est fixé sur les supports moteurs de Z et sur les bases des triangles formés par les vertex.
l’extrudeur est un i3 non modifié sauf les pignons, auquel j’ai ajouté deux carters de ventilation faits maison. Un pour refroidir la Jhead sans souffler sur la buse pour l’abs, et un carter toroïdal avec un puissant ventilateur pour refroidir la buse lors des bridges et pour le PLA.
APPROVISIONNEMENT:
Impression de toutes les pièces nécessaires et fabrication du cadre.
A partir d’une plaque d’alu de 4mm d’épaisseur, je la recouvre de scotch papier (adhesif de masquage) et je trace les découpes.
- un plan, un crayon, et la plaque masquée…
- on trace, puis on découpe a la scie sauteuse.
- le cadre brut de découpe, on va limer les bords et arrondir les angles.
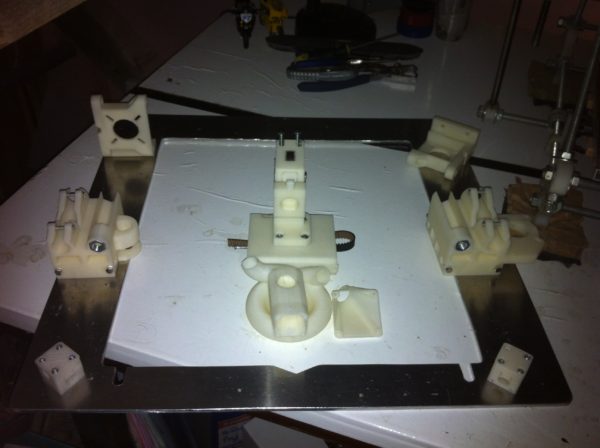
le cadre détouré et nettoyé en compagnie de toutes les pièces imprimées qu’il va falloir changer. il recevra un léger coup de belgom alu en finition une fois les fixation avec les supports moteur de Z percées.( je les ai percées cadre en place pour éviter toute erreur)
DÉMONTAGE VICTIME:
On garde le Y au complet et on ne touche pas aux vertex. Les nouveaux supports moteurs de Z sont placés sur cette photo. le cadre s’emboite par le dessous comme on peut le voir ici.
Détail du « trick » principal pour ajouter le cadre rigide sans démonter les bases du châssis:
- AVANT
- APRES
On récupère les écrous et rondelles de la fixation d’origine que l’on remplace par le nouveau clamp, celui ci peut être monté/démonté indépendamment. Le vieux clamp est découpé sans pitié… Le cadre sera fixé aux supports moteurs de Z en premier, puis réglé en bas pour être perpendiculaire aux bases.
On reviendra plus tard régler la géométrie des tiges lisses en Z (position des deux clamps visibles sur la photo ci dessus.
Ensuite on assemble le X au complet, mais sans tendre la courroie ni bloquer ses tiges lisses.
- X-end idler
- vue arriere du chariot, on peut voir ici l’utilisation de vis a tetes fraisées pour fixer l’extrudeur sans géner le passage du brin mou de la courroie. on voit également les fixations sans vis.
- Le chariot assemblé avec ses deux ventilateurs, transmission en 9×47 herringbone, et levier de chargement rapide.
- chariot assemblé. (sous un autre angle)
- X-end moteur en comparaison de son prédecesseur.
- vue de coté du X-end moteur. la courroie passe a travers. cette photo a été prise a le fin du montage on peut y voir que j’ai placé l’électronique derriere le cadre, simplement posée sur une plaque de liège.
On positionne le X sur les tiges lisses du Z et on va procéder a leur réglage, les serrer sur les supports moteurs de Z qui sont fixes et régler par le bas a l’aide des clamps. mesurer l’écartement en haut des deux tiges lisses et le reporter en bas. serrer les clamps extérieurs. maintenant on règle les nouveaux clamps, un peu plus compliqué il faut régler a la fois la parallèle des tiges lisse par rapport au cadre rigide, et la perpendicularité (ouf!) par rapport au sol dans le plan XZ. tout le monde suit?? en gros ça doit être droit dans tous les sens, re-vérifiez les précédentes mesures quand vous en modifiez une et allez y progressivement.
Remettez les moteurs de Z et leurs axes en place, et réglez le X de façon qu’il soit parallèle au plateau. à ce stade vous pouvez bloquer les tiges lisses du X et tendre la courroie.
Reste a rebrancher le tout(tel que c’était) et la machine est prête!! si vous avez bien suivi vous devez arriver à quelque chose comme ça:
Coté soft:
Il va falloir vérifier vos nouvelles dimensions du volume d’impression et les entrer dans le firmware ainsi que dans le slicer. pour info voici les miennes:
X 203mm
Y 193mm (203 avant modif, du au déport de la buse)
Z 123mm (140mm avant modif)
Notez que l’on peut gagner un peu de hauteur en Z en coupant les deux tiges filetées du haut du châssis une fois qu’elles sont maintenues par le cadre, et de « caler » les moteurs de Z pour les remonter. (en gros 2cm a gagner, je ne l’ai pas fait, préférant garder une rigidité optimale)
si comme moi vous avez changé de vis d’entrainement (hobbed bolt) ou de démultiplication (pignons) il faudra recalibrer aussi les steps/mm du moteur d’extrudeur.
TESTS ET IMPRESSIONS (les miennes, pas celles de la machine 😉 )
La partie fun, premières impressions de très bonnes qualité et châssis vraiment rigidifié, je me dis essayons plus vite: ça passe!, encore plus vite: ça passe!!! encore plus vite(en me disant ça passera pas) : CA PASSE!!!!!!!!!!
J’ai même tenté des impressions a des couches de 0.1mm, là, c’est la précision de l’extrudeur qui trouve ses limites avec sa buse de 0.5 et le filament en 3mm(et encore pour beaucoup ça paraitrait correct). mais le châssis peut le faire! actuellement j’ai des résultats optimums entre 0.15 et 0.2mm
Le carter de ventilation toroïdal fonctionne bien, juste un bémol pour les petites surfaces en hauteur, je devrais optimiser légèrement le guidage du flux. mais la ventilation est homogène autour de la buse.
Bref très content de mon upgrade, je n’ai même pas encore poussé la machine à fond mais comptant m’en servir pour produire des pièces en continu je ne préfère pas tenter le diable pour le moment, le résultat allant déjà au delà de mes espérances.
Après quelques jours, j’ai ajouté un boitier avec support adapté pour mon écran, des pieds anti vibrations (excellents), un support de bobine et un boitier pour filtre a filament.
Et quand même quelques vidéos histoire de la voir en action!!